Protecting Stainless Steel
How does metal corrosion happen?
Let’s take a look at some of the potential issues for stainless steel and corrosion. It is something many of our customers are conscious of, not just because it’s unsightly, but because it can also mean costly refurbishments or even replacements.
Firstly, all metals (including stainless steel) are covered by a very thin layer of oxide. This layer is gradually built up by chemical corrosion with the oxygen in the air. At very high temperatures, the reaction with the oxygen in the air can continue without restraint and the metal will very quickly be transformed into an oxide.
At room temperature the reaction stops when the layer is thin. These thin layers of oxide actually protect the metal against continued attack. It is the thin layers of oxide that protect the metal from continued attack to a far greater extent.

The most common forms of corrosion in stainless steel are:
- Pitting corrosion – The passive layer on stainless steel can be attacked by chemicals. The chloride ion Cl- is the most common of these and is found in everyday materials such as salt and bleach.
- Crevice corrosion – Stainless steel requires a supply of oxygen to ensure that the passive layer can form on the surface. In tight crevices, it is not always possible for the oxygen to gain access to the stainless steel surface, causing it to be vulnerable to attack. Crevice corrosion is avoided by sealing crevices with a flexible sealant.
- General corrosion – Normally, stainless steel does not corrode uniformly as ordinary carbon and alloy steels. However, with some chemicals, notably acids, the passive layer may be attacked uniformly depending on concentration and temperature.
- Galvanic corrosion – If two dissimilar metals are in contact with each other and with an electrolyte such as salt water or other solution, it is possible for a galvanic cell to be set up. This acts like a battery and accelerates corrosion. It can avoided by separating the metals with a non-metallic insulator such as rubber.
- Salt water corrosion– Due to to it’s chloride content, salty water is a most effective electrolyte. The extensive levels of oxygen present at marine locations makes these water edged environments hotspots for metal corrosion.

Is stainless steel the right choice?
Take a look at this stainless steel balustrade for example, which was installed at a sailing club, practically on the waters edge. This is a situation where corrosion is amplified, but there are a few factors in our favour. Stainless steel is a steel alloy that contains a minimum chromium content of 10.5%. As mentioned above, The chromium reacts with the oxygen in the air and forms a protective layer that makes stainless steel highly resistant to corrosion and rust. Using stainless steel here is by far the best choice (over other types of metal), and with some maintenance and care, should not rust easily, even in this type of environment.
There are also different grades of stainless steel to consider. If the steel is going to be permanently (or even partially) submerged in salt water, then you would need to consider a higher grade of stainless steel. This reduces the chance of pitting corrosion, however it is important to state that corrosion can still occur over time, due to factors such as:
- Water flow rates
- Concentration of salt (chloride) in the water
- Temperature
- Maintenance/cleaning
For examples of stainless steel grades that are available, take a look at this handy chart
More examples of stainless steel
When we are pricing a job for our customers, it is vital that we know what type of steel is suitable for any particular situation. This avoids over engineering, and thus, over pricing! Here are some examples to take a look at:



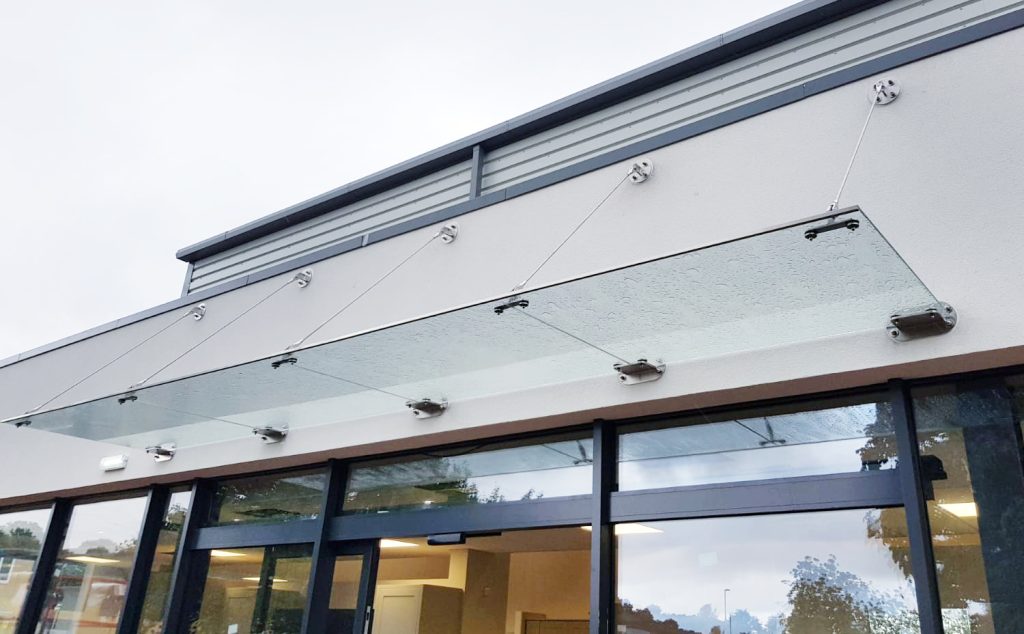
So what measures can you take to prevent corrosion in stainless steel?
- Maintenance and cleaning– stainless steel can of course corrode over time, however the beauty of this form of steel is that the corrosion is kept on the surface and can easily and efficiently be cleaned, restoring the product to its original state.
- Choosing the correct grade of steel– most of the stainless steel products we produce are made from 304 grade stainless, this grade is suitable for most scenarios, however marine grade 316 stainless is also available for jobs that require it.
- Powder coating– This is a technique used on others types of steel, and produces a textured finish on the surface of the steel. Often used in high traffic areas such as on handrails to give a more tough wearing protection to the steel beneath.
- Apply plastic coating– similar to powder coating but done with a tight fitting plastic wrap, this is an added protection that can be great for interiors.
- Looking at alternative metals– If a customer wants stainless steel, but we aren’t completely satisfied that it’s a good fit for the purpose, we may look to use alternative materials, such as galvanised steel, aluminium and GRP.
There are no assurances when using any type of metal product that corrosion in some form will happen. Taking the steps above to prevent it is the key!
Our team of qualified designers are always happy to discuss any of your queries, offer advice or supply quotes.
Get in touch to find out more.